Archive » 2017 » 2017. 01 » Kisari, Krisztián: Identifying Wastes Based on Lean Methodology in the Area of Biogas Production
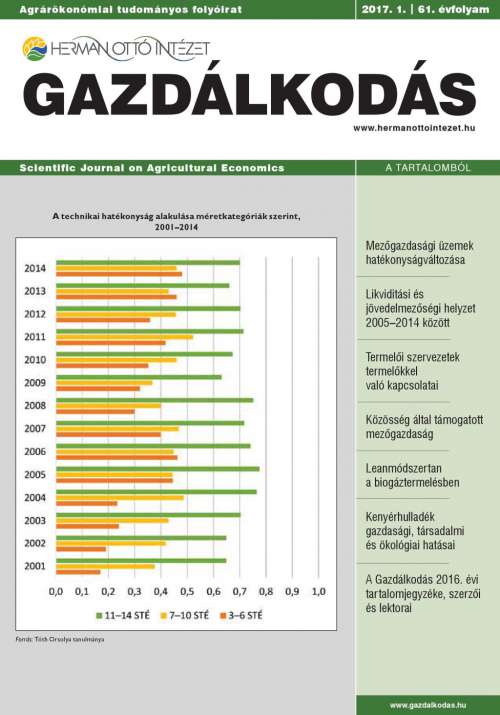
Identifying Wastes Based on Lean Methodology in the Area of Biogas Production
Kisari, Krisztián
Keywords: lean, identifying wastes, production, technological development, biogas, Q16
The study deals with the problems of biogas plants, their identifying of them and the search for possible solutions, mainly through the implementation of lean methodology in this special area. The lean, as an approach of production, has already proved its effectiveness in other industries; but in the current case a new area of use is to be represented. The operators have to face several problems which can be traced back mainly to the implementation. In Hungary the biogas plants are not highly supported, this is why they need special attention and care – and their sustainable and economical operation is still not achieved. Operating costs are progressively – in some cases, drastically – increasing. The price of commodity is continuously rising; most of the income is from the electricity production but its purchase price has fallen recently. The contravention of the strict schedule and the production, which is tied to prognosis, means a significant financial burden. In this study, the possibilities of identifying these problems, inter alia, are represented by the devices of lean. It is shown that for the loss of overproduction the change of the KÁT system or the promoting of supplying biomethane into the natural gas network could be the solution. In the case of the loss of waiting the available monitoring system should be revised (or developed, if it is not accessible) and the phenomenon of errors should be defined more precisely. The case of commodity supply can be amendable with closer cooperation with the suppliers. Transportation losses can be decreased by preferring the pipeline system and by the rationalisation of the transporting distances. The systematic revision and control of the producing process, the formation of standards, and the usage of visual management for the implementations are necessary to eliminate production losses. In the case of inventory losses, unification is needed insofar as is possible, and the preventive maintenance works, the rationalisation of the use of liquid raw materials. Unnecessary movements can be reduced with the implementation of the 5S methodology. The standardisation of the processes and the implementation of the TMP could be solutions to the elimination of waste.
Full article